The digital transformation of industry can rely on digital twins to improve production costs through optimized monitoring and quality control processes. The technical centers in the railroad industry are representative of this. Because they are responsible for both standard maintenance (preparing trains between runs) and full renewal of trains during their half-life, they face enormous constraints in terms of speed of delivery, quality control, cost control, and risk assessment.
The use of digital twins depends on two connectivity characteristics in particular: (1) high quality of experience (QoE) without any loss of connectivity, especially in mobility, i.e., operator or M2M terminal movement, and (2) accurate indoor and outdoor position tracking. The combination of these two features is a prerequisite for monitoring and automating production processes performed on the scale of an entire center (approximately 10 to 30 ha of indoor and outdoor space), as well as for risk management when tasks involving moving tools and train parts are considered.
The working environment in such manufacturing and warehousing facilities, with a typical size in the range of 10 to 30 ha, concrete and steel buildings, Faraday cages, overhead power lines and other elements with a strong impact on electromagnetic waves, is particularly complex. 5G campus networks represent an unprecedented opportunity for the digital transformation of industrial centers. They are capable of providing the QoE required for a wide range of current and future use cases. Today, rail maintenance centers use public networks when available, and in some cases deploy WLAN for indoor coverage, LPWAN networks for M2M applications, and TETRA for P2P voice communications. Despite this wide range of network choices, user satisfaction is not a given because, for example, the wireless LAN is not adapted or optimized for their mobile work patterns or for multiple access. Therefore, building a local 5G network offers them the opportunity to use a single telecommunication technology that satisfies all industrial maintenance requirements.
Mission
- Design of innovative solutions for the industry, precise and reliable geolocalization based on 5G.
- Engage a consortium involved in research, pre-industrialisation and experimentation.
- Anticipate future 3GPP releases and create evolved supervision, steering and automation tools.
- Address technological breakthroughs with impact on various types of industries in 2 major industrial countries.
- Set an experimentation platform opened to cooperations for industries in constrained, complex and secure environments.
- Involve a German industrial partner, for further applications and deployments, also with AGVs and industrial trucks manufacturers
Expected Impact
At the end of the project, the partners will have defined an optimized scenario for 5G campus networks, demonstrated their potential for monitoring and quality control management of train maintenance processes, and analyzed the possible extension in an industrial context.
Project Partners

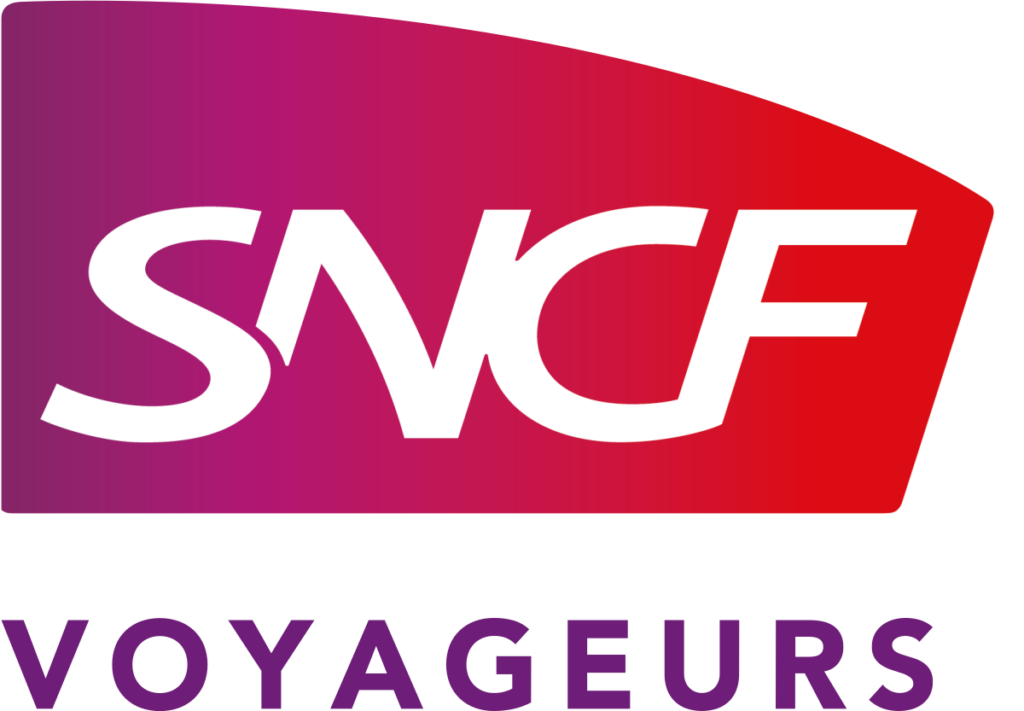
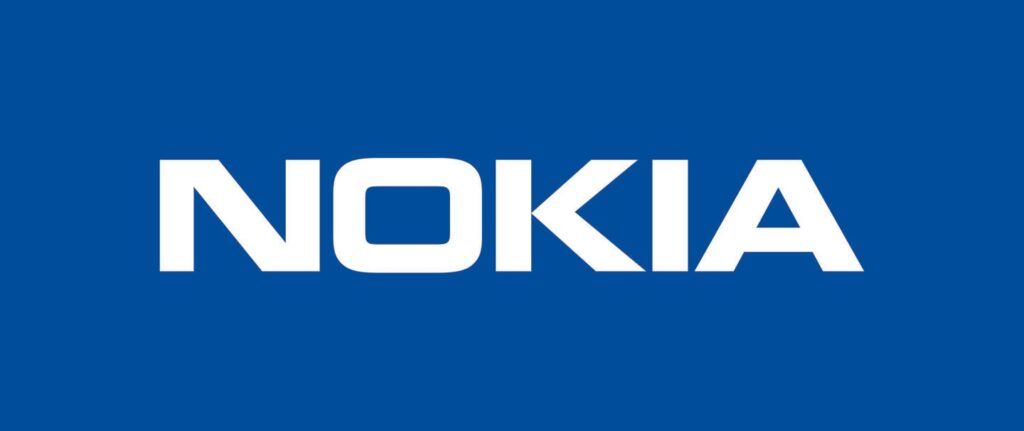
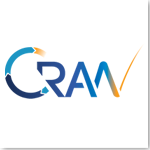